Industrial Pulse bag Dust Collector for Stone Crusher
Description
When working, the dust-laden gas enters the ash hopper from the air inlet duct, and the coarse dust particles fall directly into the bottom of the ash hopper. The gas enters the upper box to the clean gas collection pipe-exhaust duct, and is exhausted to the atmosphere through the exhaust fan. The cleaning process is to cut off the clean air outlet air duct of the chamber first, so that the cloth bag of the chamber is in a state of no air flow (the chamber is stopped to clear the dust). Then open the pulse valve and use compressed air for pulse jet cleaning. The shut-off valve is closed for a sufficient time to ensure that the dust stripped from the filter bag after the injection settles into the ash hopper, avoiding the dust from the surface of the filter bag. The phenomenon of reaching the surface of the adjacent filter bag, so that the filter bag is completely cleaned, and the exhaust valve, pulse valve and ash discharge valve are fully automatically controlled by the programmable controller.
Parameters
ITEM |
DETAIL |
Model name | BD-36 |
Fan power | 7.5KW |
Handling air volume | 5712-10562 M3/H |
Number of bags | 36 |
Filter area | 17.28 M2 |
Filter material | Polyester filament base fabric |
Cleaning method | Pulse automatic cleaning |
Noise | <=80DB |
Compressed air | 0.5-0.8Mpa |
Power supply | AC380V/50HZ |
Dimension(L*W*H) | 2260*1680*2750 |
Total Weight | 720KG |
Samples
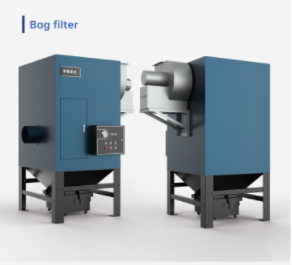
Features
1. The pulse bag filter adopts the sub-chamber air-stop pulse jet cleaning technology, which overcomes the shortcomings of the conventional pulse dust collector and the sub-chamber back-flushing dust collector.
2. Strong ash cleaning ability, high dust removal efficiency, low emission concentration, low air leakage rate, low energy consumption, low steel consumption, small footprint, stable and reliable operation, and good economic benefits.
3. The cleaning cycle is prolonged, which reduces the energy consumption of cleaning, and the consumption of compressed air can be greatly reduced. The fatigue level of the filter bag and pulse valve is also reduced accordingly, thereby multiplying the life of the filter bag and valve plate.
4. The maintenance and replacement of bags can be carried out in separate rooms under the normal operating conditions of the system without stopping the system fan.
5. The mouth of the filter bag adopts an elastic expansion ring, which has good sealing performance and is firm and reliable. The filter bag keel adopts polygonal shape, which reduces the friction between the bag and the keel, prolongs the life of the bag, and facilitates the unloading of the bag.
6. The upper part of the bag is drawn. After the skeleton is pulled out when changing the bag, the dirty bag is put into the ash hopper at the lower part of the box and taken out from the manhole, which improves the operating conditions of changing the bag.
7. The box body adopts air-tight design, which has good sealing performance. The inspection door uses excellent sealing material. During the production process, kerosene is used to detect leakage, and the air leakage rate is very low.
8. The inlet and outlet air ducts are compactly arranged, and the airflow resistance is small.
Application
Flue gas treatment and dust removal systems in iron plants, steel plants, ferroalloy plants, refractory plants, foundries, power plants, etc. Flue gas filtration of waste incinerators, coal-fired boilers, fluidized bed boilers, etc. Asphalt concrete mixing, building materials, cement ceramics, lime, gypsum and other production sites. Aluminum electrolysis, smelting flue gas filtration of lead, tin, zinc, copper and other rare metals, fine material recovery, liquid and solid separation. Liquid-solid separation and fine material recovery in chemical, coke, carbon black, dye, pharmaceutical, plastic and other fields. Dust control and purification collection for mining, grain processing, flour, electronics industry, wood processing, etc.
Details
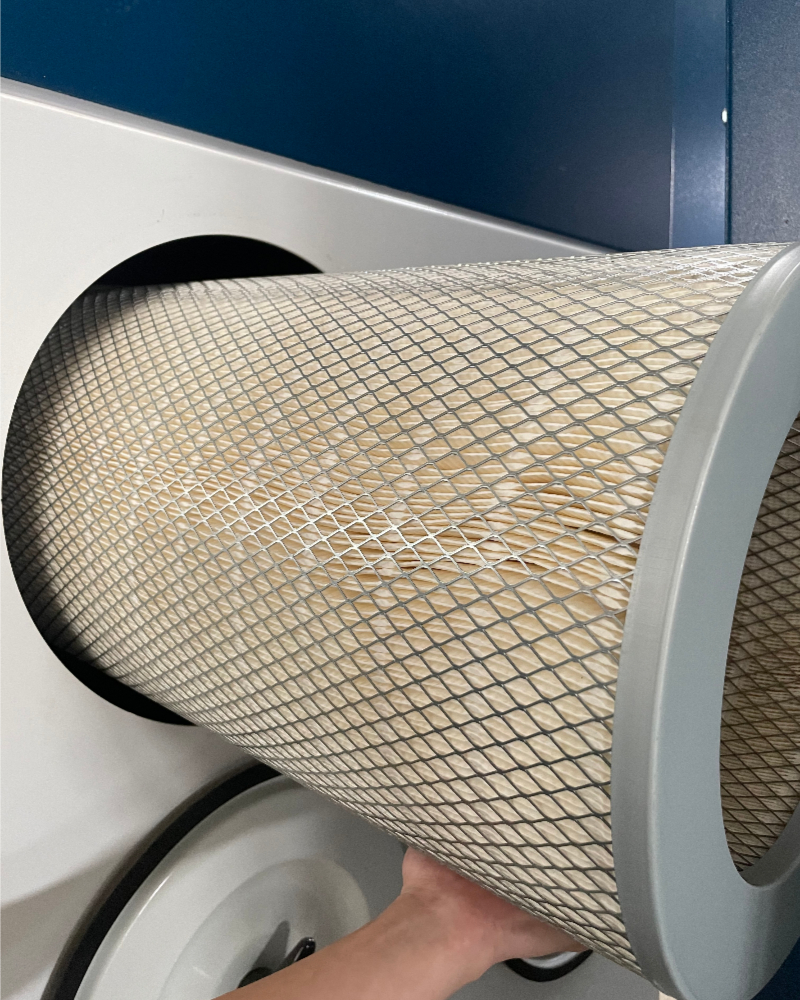
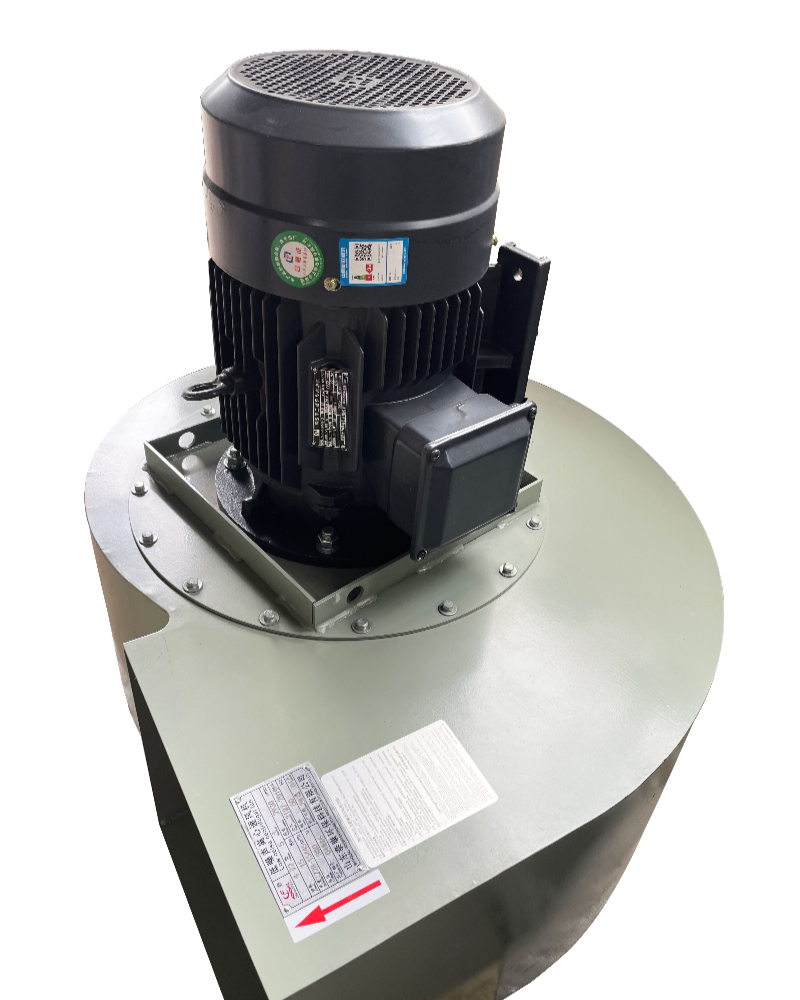
